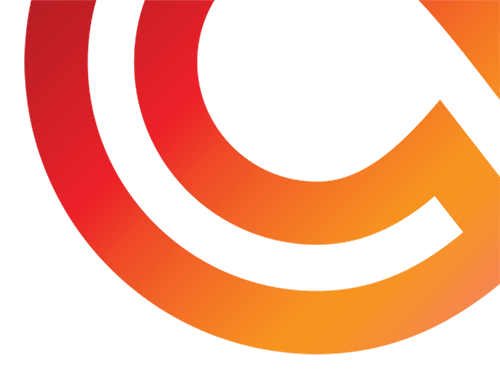
Automotive Logistics
Lean Manufacturing in Automotive Logistics
Crown SDS’ automotive logistics service is designed around improving efficiencies and problem solving for customers. Supporting our customers to implement lean processes; which in turn improve safety, reduce costs, increase production and flexibility, among the many other benefits, demonstrate how we are more than a same day courier service.
Simply put, any process that does not add value for a business can be deemed wasteful. We work collaboratively with our customers to reduce waste within their warehousing and transportation processes.
The Challenge:
The customer, a multinational vehicle manufacturer with a distribution facility in Lutterworth, required support from Crown SDS to create a more efficient process for moving automotive parts between its warehouse and delivery vans.
But more than just reducing waste, the customer needed a long-term process that could continue to support despite demand fluctuations and any other factor that could have an impact on distribution.
The Solution:
Crown SDS undertake a collaborative approach when working with our customers, to ensure we understand their business and its long-term goals. Part of creating logistics and courier solutions requires discussing with the customer their expectations and to study their existing supply chain processes.
Applying a Kaizen approach, we were able to create an action plan that would create long-term value through changing culture and ultimately, implementing a truly effective continuous improvement programme.
Existing Issues:
- The sorting of small, medium and large stock parts was uncontrolled, meaning there was no way to ensure the right parts were picked and delivery paperwork was being completed correctly.
- Products were moved from warehouse to van using a shopping trolley, an inefficient and wasteful process across an area that was untidy and posed health and safety issues.
- Process of delivery waves (i.e. the different timings of deliveries to the automotive dealerships) was not very efficient, with shorter distance deliveries being scheduled to take place first. This meant longer distances deliveries were being left until last to be dispatched.
New Process:
- Controlled sort area introduced to ensure stock and delivery paperwork were more efficiently managed.
- Review of trolley used for parts movement to introduce new equipment and enhance health and safety, quality, delivery and more.
- Improve booking of deliveries and the way routes are controlled. Crown SDS implemented 5 delivery waves, increased from the previous 3 waves, to smoothen and streamline the delivery process. Routes were also redesigned dynamically, so that longer distance deliveries would be scheduled to go ahead first, followed by shorter distance deliveries.
The Impact:
- New controlled sort area ensures parts are checked off against the paperwork, providing enhanced visibility of routes, van sizes, driver identification, stock and loose parts. This gives better control of stock and reduces loss of assets.
- Increased number of delivery waves to provide a longer window with which dealerships can order automotive parts for same day delivery, with no disruption to delivery times.
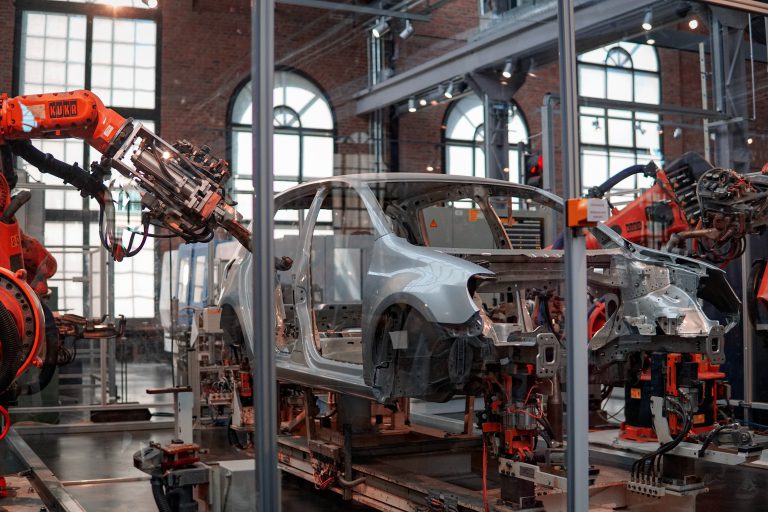